
3.1.2 For non-expanding steel structure fire-resistant coatings, it is advisable to use an epoxy zinc-rich primer for the bottom layer.
3.1.3 Before construction, mask and protect areas and objects that do not require spraying.
IV. Construction Process
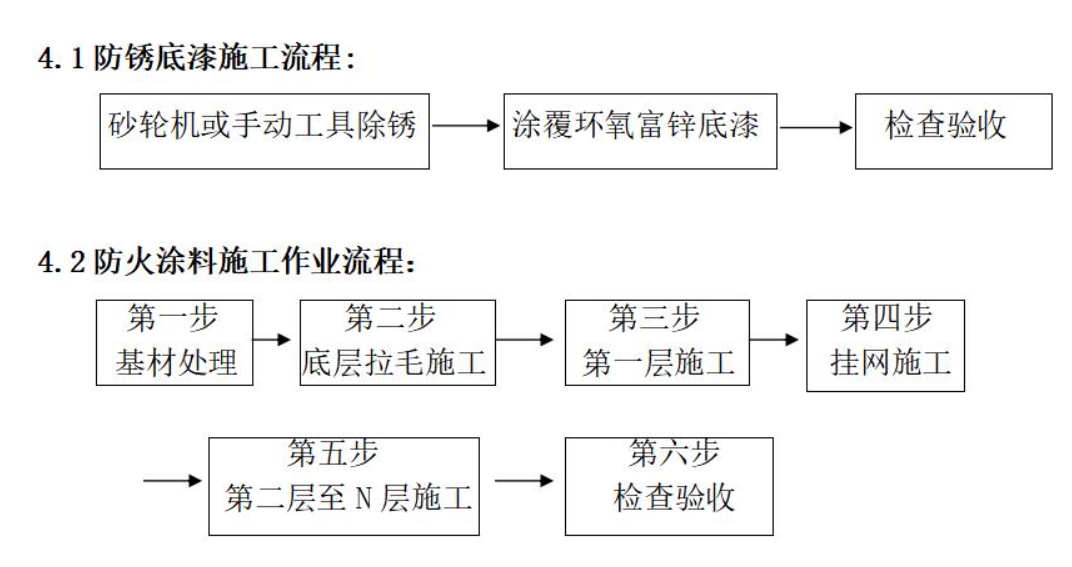
V. Construction Steps
5.1 Steel Structure Surface Treatment
5.1.1 Use a grinder or hand tools to polish the steel structure surface, use cotton cloth or a clean bristle brush to remove dust, and clean oil stains with a cleaning agent.
5.1.2 Welding joints should be treated as a priority. Remove weld spatter, scale, and rust with a steel shovel, scraper, steel brush, or grinder. The rust removal level should reach the St2 standard.
5.1.3 The treated steel structure base layer should be primed within 4 hours. When the steel structure is stored indoors, it should not exceed 16 hours. When the relative humidity is greater than 75%, the interval time should be shortened.
5.1.4 Acceptance must be completed before anti-rust primer construction.
5.2 Anti-rust Primer Application
5.2.1 Before application, the treated surface should be cleaned to remove dust and debris. After inspection and approval, the anti-rust primer can be applied.
5.2.2 Construction temperature and humidity should meet the requirements of the instructions. If it rains, fogs, or there is strong wind, outdoor construction should not be carried out, and protective measures should be taken for the constructed areas.
5.2.3 Epoxy zinc-rich primer is a two-component paint. The mixing ratio is 10:1. Fully stir component A and add component B, continuing to stir until uniform. The curing time is 20 minutes (20℃), and the usable time is 4 hours (20℃). According to the viscosity requirements of the site, add 0-20% of the special thinner for dilution. After the first coat of anti-rust primer is surface-dry, the next coat can be applied.
5.2.4 All painted areas must not be missed. The coating surface should be smooth and flat, with consistent color, and no pinholes, bubbles, sagging, cracking, or damage.
5.2.5 The total thickness of the dry film coating is 60-90μm. The thickness of each coat should be checked with a film thickness gauge to ensure it meets the design requirements.
5.3 Quality Inspection
5.3.1 Appearance Inspection: The coating should be smooth and flat, with consistent color, and no pinholes, bubbles, sagging, cracking, or damage.
5.3.2 Primer Thickness Inspection: Use a magnetic thickness gauge to check. The primer thickness should be uniform, and the primer thickness and number of layers should meet the design requirements.
5.3.3 Use the finger touch method to determine whether the coating is surface-dry, and use the blade method to determine the fully dry condition of the coating. The primer must be completely dry before applying the fire-resistant coating.
5.4 Fire-resistant Coating Construction
5.4.1 Construction can only proceed when the rust removal and anti-rust treatment of the steel structure surface meet the requirements, and dust and other debris have been removed.
5.4.2 Spraying or troweling methods can be used. It is recommended to use spraying for large-area steel beams and columns, and troweling for small areas such as channel steel and tie rods. If spraying is used, a self-weight spray gun can be used. The diameter of the spray gun nozzle is 6-10mm, the air pump working pressure is 0.4-0.8Mpa, and the vertical distance between the spray gun and the substrate surface is 300-500mm.
5.4.3 Construction of the first layer of fire-resistant coating: Before spraying or troweling the non-expanding steel structure fire-resistant coating, a base coat must be applied (the base coat should be sprayed to avoid air pockets. If spraying is not allowed on site, roller coating can be used. The surface of the fire-resistant coating applied using the roller coating method should be roughened. The steel structure should not have any exposed areas, which is beneficial for bonding with the next layer of fire-resistant coating). The base coat mixing ratio is:
Non-expanding steel structure fire-resistant coating: 707 emulsion: water = 1:0.25:0.8~1 (100 kg of powder material adds 25 kg of 707 emulsion, the amount of water can be increased or decreased appropriately according to the construction needs). Mixing method: First add water to the mixer, then add the measured 707 emulsion to the mixer, and stir for about 2~3 minutes; then add the non-expanding steel structure fire-resistant coating and stir until uniform (10-15 minutes), the time should not be too long (Note: The amount of water can be adjusted appropriately to suit the construction). The base coat is sprayed using a hand-held spray gun or roller-coated, with a thickness of 1.5~2.0mm, not too thin or too thick, the bottom layer is basically uniform, and there should be no exposed steel structure surface. The mixed coating should be used up within 2 hours, and the next manual application can be carried out after 24 hours (after it is completely solidified and hardened).
5.4.4 Construction of the second to nth layer of fire-resistant coating: The mixing ratio of the coating is non-expanding steel structure fire-resistant coating: water = 1:1, using low-speed stirring, stir until uniform (10-15 minutes), do not stir for too long, just mix well. The second and subsequent layers of fire-resistant coating can be applied by spraying or troweling. The second layer of fire-resistant coating should be applied when the first layer is 7-80% dry (about 24 hours later); if the drying time of the first layer is too long, spray water appropriately before the second application. The thickness of each layer can be 8~10mm, until the fire-resistant design thickness is reached. The interval time between two applications is 24 hours, not too long or too short, and the mixed material should be used up within 2 hours each time. During interlayer construction, the surface of the fire-resistant coating should not be smoothed, and a rough surface can be made, which is beneficial for bonding between the upper and lower layers.
5.4.5 During summer high temperatures or if the application interval is too long, water spraying maintenance should be carried out to prevent the coating from cracking, delamination, and powdering due to water loss; once the packaging is opened, it should be used immediately. If the coating is found to be damp or caked, it should not be used; Construction environment: During construction and within 24 hours after construction, the ambient temperature should not be lower than 5℃. Like all cement mortars, it will be damaged by freezing before solidification. However, under extremely dry and hot conditions, necessary curing conditions should be created to prevent the coating from losing water too quickly (such as shading and water spraying measures).
5.4.6 When the coating thickness is equal to or greater than 20mm, when the second coat of non-expanding steel structure fire-resistant coating (coating thickness is about 8-10mm) is applied, glass fiber mesh should be laid. The specifications should use wire diameter φ0.5mm—φ1.5mm, mesh size 10mmx10mm; the coating corners can be made into right angles or arcs with a radius of 10mm. According to the actual situation of different specifications of steel structures on site, the mesh is cut into reasonable lengths. When hanging the mesh, pay attention to the pressing of the concave and convex corners of the steel, do not protrude too much, and there should be a gap of about 8mm-10mm between the glass fiber mesh and the steel structure. The overlapping length of the mesh is 50-100mm. The cut glass fiber mesh can be pressed flat on the slurry.
5.4.7 When constructing the skirt base and the top of the steel structure, a 30º-45º bevel should be made for the fire-resistant coating. After the coating is dry, the top of the bevel must be sealed with outdoor sealant.
(The method is shown in the figure below)
5.4.8 The construction personnel should use a thickness gauge to detect the coating thickness and ensure that the coating thickness meets the design requirements.
5.4.9 When the coating reaches the design thickness, the last coat should be smoothed to ensure a uniform and flat surface.
5.5 Quality Inspection
5.5.1 Use visual inspection to check whether the coating color is consistent with the selected sample.
5.5.2 Use a thickness gauge to measure different points (no less than 5 points per square meter) to check whether the coating thickness meets the design requirements.
5.5.3 Check whether there are any omissions, powdering, or obvious cracks in the coating. If there are individual cracks, they should be repaired immediately.
5.5.4 Use a 0.75-1㎏ hammer to lightly tap the coating to check its strength, and use a 1m flat ruler to check the surface flatness.
5.6 Maintenance
5.6.1 After the fire-resistant coating is completed, rain, vibration, and sun exposure protection measures should be taken.
5.6.2 After the product is formed, in places with conditions, water spraying maintenance or other maintenance measures can be used to maintain the product.
5.7 Coating Construction Precautions
5.7.1 In northern regions with large temperature differences, steel components must be treated with metal mesh. In coastal humid areas, the fire-resistant coating should be protected.
5.7.2 Construction of this product is not suitable when the winter ambient temperature is below 5℃; construction is not suitable when the surface temperature of the substrate is above 50℃ in summer.
5.7.3 In the rainy season, the newly constructed fire-resistant coating should be protected from rain.
5.7.4 Work should not be carried out when the wind speed is greater than 5m/s, or in rainy days and when there is condensation on the surface of the components.
5.7.5 Pay attention to the coating thickness of the first layer.
5.7.6 When the construction of the fire-resistant coating needs to be interrupted or the coating needs to be repaired due to certain reasons, a 30-40° slope should be left as a bonding surface for the next construction or repair. Before construction or repair, the slope should be cleaned and moistened to ensure good bonding between the old and new surfaces.
5.7.7 Non-expanding steel structure fire-resistant coatings should be protected from rain and moisture during transportation and storage. If the fire-resistant coating is solidified and caked, it should not be used.
5.7.8 After each construction is completed, the equipment and tools used should be cleaned immediately with clean water.
5.7.9 When there is three-dimensional cross-operation during construction, safety should be paid attention to.
VI. Quality Control Measures and Quality Assurance System
6.1 Construction Management Process
The entire steel structure fire-resistant coating project should be subject to full-process quality management. The quality management system should include:
A. Preparation work;
B. Technical briefing;
C. Combination of fire-resistant coating spraying and troweling;
D. Quality evaluation;
E. Document organization.
6.2 Specific Quality Requirements
6.2.1 Consistent appearance and color, meeting design and contract requirements.
6.2.2 The fire-resistant coating thickness meets the specified requirements.
6.2.3 No cracks on the coating surface.
6.2.4 Flat surface, no obvious depressions, firm adhesion, no powdering, loosening, or floating slurry.
6.2.5 Complete product test reports.
6.3 Quality Assurance Measures
6.3.1 Assign a dedicated quality inspector to be responsible for inspection and quality control.
6.3.2 Carefully read the product instructions and implement the construction plan during construction.
6.3.3 Strictly inspect after opening, verifying the product model, type, and color.
6.3.4 Strict self-inspection, checking and testing at any time, and keeping good records.
6.3.5 The preparation and mixing of coatings must be handled by a dedicated person.
6.3.6 Fill in the construction records in detail, including ambient temperature, humidity, and construction conditions.
6.3.7 Cooperate with the project client to complete quality visa applications.
6.4 Quality Inspection
6.4.1 Thickness: Thickness is measured using a thickness gauge.
6.4.2 Color: Visual inspection, according to the design and color card or sample.
6.4.3 Cracks: Visual inspection or measurement with a steel ruler, referring to standard CECS24-90.
6.4.4 Adhesion: Gently tap the coating surface with a 0.5~1kg hammer; no shedding should occur.
6.4.5 Coating Appearance: Visual inspection.
6.5 Quality Control Measures
6.5.1 Organize on-site quality inspectors and relevant construction management personnel to hold a special quality management meeting, study relevant quality documents and standards, and formulate quality management systems.
6.5.2 Strictly implement self-inspection, exceeding standards but never falling below them. Actively and promptly invite the project supervisor for on-site inspection.
6.5.3 Before coating, verify the model, name, and color of the product. Check the manufacturing date and product qualification certificate. The mixing ratio and stirring of the paint should be handled by a designated person, and monitoring records should be kept for the files.
6.5.4 If quality accidents occur, analyze the specific causes, fill out a quality accident investigation report, provide corrective measures, and promptly carry out repairs.
6.5.5 The project quality inspector should report the construction quality situation to the project manager at any time and fill out quality records, reflecting the construction quality situation in detail.

Indoor non-expanding steel structure fire-retardant coating 3.0
Contact Us
Belonging Category
Related Products
Product Inquiry